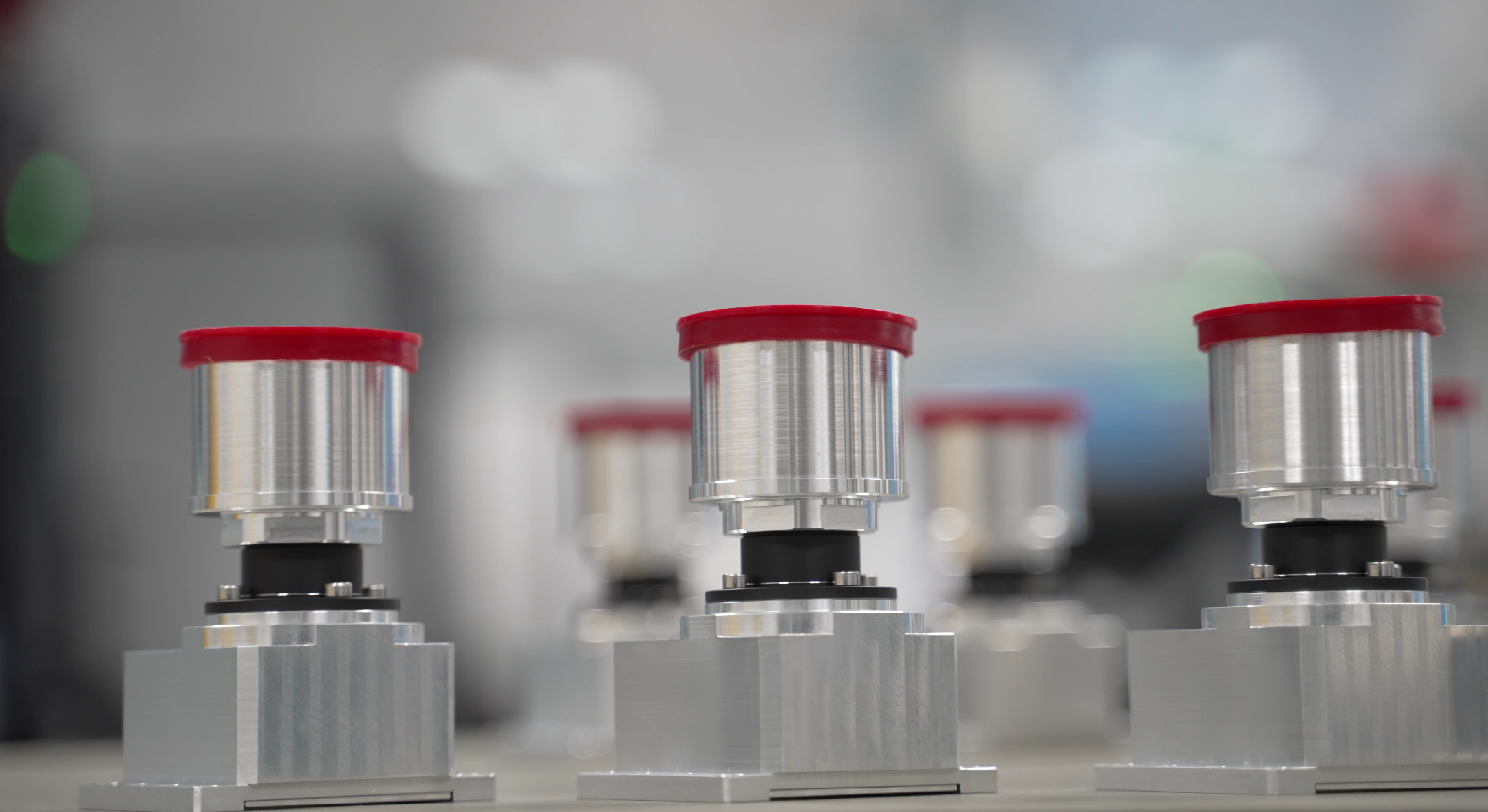
In this paper, we will explain how the electronic components and the image sensors for our star trackers are selected, in order to propose the best performance/lifetime/price trade-off, while offering resistance to radiation.
The lead time and the ability to deliver satellite equipment, including star trackers, has now come down to just a few weeks, driven by the changing economic constraints of NewSpace. In a context such as this, how do we propose high-quality products meeting the requirements in such a short period of time?
- The changing requirements of NewSpace
In 2019, SODERN was the world’s first equipment manufacturer to produce and market a reliable, compact, standardized, off-the-shelf star tracker. It was initially intended for the OneWeb constellation, but in fact revolutionized the NewSpace market. The need for small, high-performance and accessible star trackers with a short delivery lead time, rapidly expanded to include all manufacturers of 6U to 500kg satellites.
The design of Auriga™ took account of 4 fundamental criteria: compactness, robustness across the entire celestial vault, the ability to produce several thousand items a year, and resistance to radiation, thus guaranteeing mission lifetimes of up to 10 years in LEO and 15 years in GEO.
- Reliable industrial production to guarantee the best possible products
When initial design work began on the Auriga™ star tracker, SODERN made its ability to deliver 2,000 trackers a year the focus of its strategy. To do this, right from the product design stage, it had to define its industrialization process, choosing the most robust and agile supply chain possible. The company thus made the decision not to use components from Hi-Rel foundries, but to upscreen automotive grade components, although with no compromise on reliability.
This decision guarantees that customers have access to a competitive product based on a supply chain that is familiar with high volumes and short lead times.
How? For more than 60 years now, SODERN, Société d’Etudes et de Réalisations Nucléaires, has developed unique in-house skills in the study and analysis of radiation phenomena, with a team of recognized experts, notably physicists with expertise in fundamental interactions and elementary particles. This also makes SODERN a world-class supplier of neutron sources.
These core skills have enabled us to take part in the design of iconic space missions in extreme radiation environments, with demanding customers. Prime examples are missions to the environment of Jupiter, namely Juice (specialized navigation cameras and Hydra star trackers) and Europa Clipper (Hydra star trackers with radiation hardening modifications). This expertise helped us determine that 35-krad tolerant electronics are ideal for customers whose LEO, MEO, GEO missions do not generally exceed 15 years.
- All the electronic components and image sensors used are upscreened.
The image sensor and all the electronic components used in the Auriga™ star tracker are upscreened. They undergo a rigorous selection, notably by means of systematic high-temperature burn-in stress test, and electrical characterizations across the equipment’s entire operating temperature range. Components failing the screening criteria are rejected, and will not be used for production. This selection process guarantees the superior reliability of the equipment produced. In the same way, all the procured component batches are subjected to radiation and environmental tests, ensuring their build quality and their ability to withstand an ionizing dose level of 35 krad.
If we look a little more closely, concerning a mission lifetime of 15 years, the primary radiation phenomenon which reduces performance – and therefore potentially the lifetime of the mission – tends to be displacement damage caused by protons. The effect is to impair the detector’s performance by degrading its signal-to-noise ratio, regardless of the detector’s tolerance to total ionizing dose.
The key was thus to develop proprietary image pre-processing algorithms associated with locally sourced electronics to compensate for this damage. Another solution, which is far more costly in terms of power consumption, would have been to cool down the image sensor, an option that was ruled out by SODERN. Next, the choice of an image sensor with small pixels and compact photodiodes, unlike most of the star trackers from the competition, was crucial. This is also because the smaller the photodiodes, the lower the detector’s sensitivity to proton-induced displacement damage.
- What criteria should be used to evaluate radiation resistance?
In short, the level of tolerance to the ionizing dose, often expressed in krad in the datasheets, or the use of a space grade foundry, do not in guarantee by themselves the overall resistance to radiation effects. For most missions lasting less than 15 years, the limiting factor with the greatest impact will be proton-induced displacement damage. A high-reliability detector capable of tolerating 35 krad will therefore, in most cases, be a better option than a detector able to withstand 100 krad but with lower proton resistance and without appropriate and powerful image pre-processing algorithms.
Since 2019 and building on these compromises, more than 1,250 satellites have been equipped with SODERN star trackers, racking up more than 30 million flight hours with 100% mission success. Backed by its supply chain and its technological advances, SODERN delivers an average of 400 Auriga™ star trackers around the world every year (excluding constellations), with a lead time of less than 1 month.